什么是晶圆的切割划片技术
转载来源:芯片技术与工艺
作者 | 北湾南巷
出品 | 芯片技术与工艺
晶圆切割划片技术作为半导体制造流程中的关键环节,其技术水平直接关联到芯片的性能、良率及生产成本。
#01
晶圆切割的背景与意义
1.1 晶圆切割的定义
晶圆切割(或称划片)是半导体制造流程中的重要环节,其目的是将经过多道工序处理的晶圆分割成多个独立的晶粒。这些晶粒通常含有完整的电路功能,是最终用于制造电子产品的核心组件。随着芯片设计复杂度和尺寸的缩小,对晶圆切割技术的精度和效率要求也越来越高。
在实际操作中,晶圆切割通常采用金刚石刀片等高精度切割工具,以确保每个晶粒保持完整、功能正常。切割前的准备、切割过程中的精确控制及切割后的质量检测均是关键环节。其中,切割前需要对晶圆进行标记和定位,确保切割路径准确无误;切割过程中,需要对刀具的压力、速度等参数进行严格控制,以防止损坏晶圆;切割后还需进行全面的质量检测,确保每一颗芯片符合性能标准。 晶圆切割划片技术的基本原理不仅仅包括切割设备的选择和工艺参数的设置,还涉及到材料的力学性能和材料特性对切割质量的影响。例如,低-k介质硅晶圆因其力学性能较差,在切割过程中极易受到应力集中影响,从而引发崩裂、裂纹等失效问题。低-k材料的低硬度和脆性使其在受到机械力或热应力时更容易发生结构破坏,特别是在切割过程中,刀具与晶圆表面的接触和高温会进一步加剧应力集中。
随着材料科学的进步,晶圆切割技术不仅应用于传统硅基半导体,还扩展至氮化镓等新型半导体材料。这些新材料由于其硬度和结构特性,给切割工艺带来了新的挑战,需要进一步改进切割工具和技术。
晶圆切割作为半导体产业中的关键工艺,随着需求的变化和技术的进步,仍在不断优化,为未来的微电子和集成电路技术奠定基础。除了辅助材料和工具的开发,晶圆切割技术的改进还涵盖了工艺流程优化、设备性能提升以及切割参数的精确控制等多个方面。这些改进旨在确保晶圆切割过程的高精度、高效率和稳定性,以满足半导体行业对更小尺寸、更高集成度和更复杂结构芯片的需求。
提升方向 |
具体内容 |
效果 |
工艺流程优化 |
- 改进前期准备,如更精确的晶圆定位与路径规划。 |
- 减少切割误差,提升稳定性。 |
- 采用实时监控与反馈机制,调整切割过程中刀具的压力、速度与温度。 |
- 降低晶圆破损率,提高芯片质量。 |
设备性能提升 |
- 应用高精度机械系统与先进的自动化控制技术。 |
- 提高切割精度,减少材料损耗。 |
- 引入激光切割技术,适用于高硬度材料晶圆。 |
- 提高生产效率,减少人工误差。 |
- 提升设备自动化程度,实现自动监控与调整。 |
|
切割参数精确控制 |
- 对切割深度、速度、刀具类型、冷却方式等参数进行精细调整。 |
- 确保晶粒完整性和电气性能。 |
- 根据晶圆材料、厚度、结构进行参数定制。 |
- 提高成品率,减少材料浪费与生产成本。 |
战略意义 |
- 持续探索新技术路径,优化工艺流程,提升设备能力,以应对半导体市场需求。 |
- 提高芯片制造的良率与性能,支持新材料和先进芯片设计的技术发展 |
1.2 晶圆切割的重要性
晶圆切割在半导体制造流程中扮演着关键角色,直接影响后续工序以及最终产品的质量和性能。以下从几个方面详细说明晶圆切割的重要性。
首先,切割精准度和一致性是确保芯片成品率和可靠性的关键。在制造过程中,晶圆经过多道工序后形成了多个微小电路结构,需要精确划分为独立的芯片(晶粒)。如果切割过程中的定位或切割误差较大,可能导致电路受损,进而影响芯片的功能与可靠性。因此,高精度的切割技术不仅能保证每颗芯片保持完整性,还能避免芯片内部电路损坏,提高成品率。
其次,晶圆切割对生产效率和成本控制有着显著影响。晶圆切割作为制造流程中的重要步骤,其效率直接影响后续工序的进度。通过优化切割工艺,提高设备的自动化程度和切割速度,可以显著提升整体生产效率。另一方面,切割时的材料损耗也是企业控制成本的重要环节。使用先进的切割技术不仅能减少切割过程中不必要的材料浪费,还能提高晶圆的利用率,进而降低生产成本。
随着半导体技术的进步,晶圆的直径不断增大,电路密度也随之增加,这对切割技术提出了更高的要求。大尺寸晶圆需要更加精确的切割路径控制,尤其是在高密度电路区域,任何细小的偏差都可能导致多个芯片失效。此外,更大的晶圆意味着更多的切割线和更复杂的工艺步骤,切割技术必须进一步提升其精准度、一致性和效率,以应对这些挑战。
1.3 晶圆切割的工艺流程
晶圆切割的工艺流程涵盖了从准备阶段到最终的质量检查,每个步骤都至关重要,以确保切割后的芯片质量和性能。以下是对各个阶段的详细阐述。
阶段 |
详细描述 |
准备阶段 |
- 清洗晶圆:使用高纯度水和专业清洗剂,结合超声波或机械擦洗,去除杂质、微粒和污染物,确保表面洁净。 |
- 精确定位:依赖高精度设备,确保晶圆能够按照设计好的切割路线准确划分。 |
- 固定晶圆:将晶圆固定在胶带框架上,确保其在切割过程中稳定,避免因振动或移动受损。 |
切割阶段 |
- 砂轮划片:利用高速旋转的金刚石涂层刀片进行物理切割,适合硅基材料,成本较低。 |
- 激光划片:高能激光束进行非接触式切割,适用于脆弱或高硬度材料,如氮化镓,精度更高,损耗更小。 |
- 新技术引入:激光和等离子切割技术进一步提高了切割效率和精度,减少热影响区域。 |
清洗阶段 |
- 使用去离子水(DI水)和专用清洗剂,结合超声波或喷淋清洗,清除切割过程中产生的碎屑和粉尘,防止残留物影响后续工艺或芯片电性能。高纯度的DI水避免引入新的污染物,确保晶圆的洁净环境。 |
检查阶段 |
- 光学检测:通过光学检测系统结合AI算法,快速识别缺陷,确保切割后芯片无裂纹、缺角等问题,提高检测效率并减少人工误差。 |
- 尺寸测量:确认芯片尺寸符合设计要求。 |
- 电性能测试:确保关键芯片的电学性能符合标准,保证其后续应用中的可靠性。 |
分拣阶段 |
- 通过机械臂或真空吸盘将合格的芯片从胶带框架上分拣出来,并根据性能自动分类,确保生产效率和灵活性,进一步提高精准度。 |
晶圆切割流程涉及晶圆清洗、定位、切割、清洗、检测和分拣,每一个步骤都至关重要。随着自动化、激光切割、AI检测技术的进步,现代晶圆切割系统能实现更高的精度、速度和更低的损耗。未来,激光和等离子等新型切割技术将逐步取代传统刀片切割,以适应更复杂的芯片设计需求,进一步推动半导体制造工艺的发展。
#02
晶圆切割技术及其原理
图中展示了三种常见的晶圆切割技术,分别为机械刀片划片(Blade Dicing)、激光划片(Laser Dicing)和等离子切割(Plasma Dicing)。下面对这三种技术进行详细解析并补充说明:
在半导体制造过程中,晶圆的切割是一个关键步骤,它要求根据晶圆的厚度选择合适的切割方法。首先,需要判断晶圆的厚度。如果晶圆的厚度超过100微米,可以选择刀片切割方法进行切割。如果刀片切割不适用,可以转向断裂切割法,该方法包括划痕切割和刀片切割两种方式。
当晶圆的厚度在30至100微米之间时,推荐使用DBG(Dice Before Grinding,即先切割再研磨)的方法。在这种情况下,可以选择划痕切割、刀片切割,或者根据需要改变切割顺序以达到最佳效果。
对于厚度小于30微米的超薄晶圆,激光切割成为首选方法,因为它能够精确地切割薄晶圆而不会造成过多的损伤。如果激光切割无法满足特定要求,可以采用等离子体切割方法作为替代方案。这个流程图提供了一个明确的决策路径,确保在不同厚度条件下选择最合适的晶圆切割技术。
2.1 机械切割技术
机械切割技术是晶圆切割中的传统方法,其核心原理是利用高速旋转的金刚石砂轮划切刀具对晶圆进行切割。关键设备包括空气静压主轴,它通过高速驱动金刚石砂轮刀具,沿预设的切割路径进行精确切割或开槽操作。该技术因其低成本、高效率及广泛的适用性,成为行业内广泛使用的方案。
优势
金刚石砂轮刀具的高硬度与耐磨性使得机械切割技术能够适应多种晶圆材料的切割需求,不论是传统的硅基材料,还是新型的化合物半导体。其操作简单,技术要求相对较低,进一步推动了其在大规模生产中的普及。此外,该技术相较于其他切割方式,如激光切割,成本更为可控,适合企业在批量生产中的需求。
局限性
尽管机械切割技术具有众多优点,但其局限性同样不可忽视。首先,由于刀具与晶圆的物理接触,其切割精度相对有限,容易产生尺寸偏差,影响芯片后续封装和测试的准确性。其次,机械切割过程中易产生崩边、裂纹等缺陷,这些缺陷不仅影响成品率,还可能对芯片的可靠性和使用寿命造成负面影响。这种机械应力引发的损伤对高密度芯片制造尤为不利,特别是在切割较脆的材料时,这些问题更加突出。
技术改进
为了克服这些局限,研究人员不断对机械切割工艺进行优化。通过改进砂轮刀具的设计与材料选择,提升其切割精度和耐用性是一项重要的改进措施。此外,优化切割设备的结构设计与控制系统,进一步提升了切割过程的稳定性与自动化水平。这些改进减少了人为操作导致的误差,提升了切割的一致性。引入先进的检测与质量控制技术,实时监控切割过程中的异常情况,也有效提高了切割的可靠性和成品率。
未来发展与新技术
尽管机械切割技术仍然在晶圆切割领域占据重要地位,随着半导体工艺的进步,新的切割技术也在快速发展。例如,热激光切割技术的应用为解决机械切割中的精度和缺陷问题提供了新的思路。这种非接触式的切割方式能够减少物理应力对晶圆的影响,大幅降低崩边和裂纹的发生率,尤其适用于切割脆性较高的材料。未来,机械切割技术与新兴切割技术的结合,将为半导体制造提供更广泛的选择和灵活性,进一步提升芯片的制造效率与质量。
综上所述,机械切割技术尽管存在一定的缺点,但通过持续的技术改进和与新型切割技术的结合,依然在半导体制造中发挥重要作用,并有望在未来工艺中保持其竞争力。
2.2 激光切割技术
激光切割技术作为晶圆切割中的新型方法,因其高精度、无机械接触损伤以及快速切割等特点,逐渐在半导体行业中受到广泛关注。该技术利用激光束的高能量密度和聚焦能力,在晶圆材料表面形成微小的热影响区。当激光束作用于晶圆时,产生的热应力会引发材料在预定位置断裂,达到精确切割的效果
激光切割技术的优势
- 高精度:激光束的精准定位能力可实现微米甚至纳米级的切割精度,满足现代高精度、高密度集成电路制造的要求。
- 无机械接触:激光切割无需接触晶圆,避免了机械切割时常见的崩边、裂纹等问题,显著提高了芯片的成品率和可靠性。
- 切割速度快:激光切割的高速度有助于提升生产效率,尤其适用于大规模、高速生产的场景。
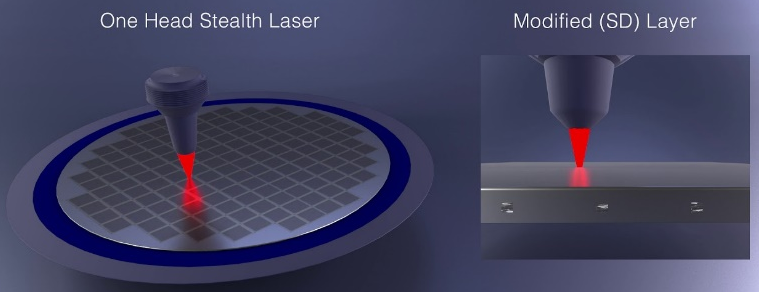
面临的挑战
- 设备成本高:激光切割设备的初期投资较高,尤其对于中小规模生产企业而言,推广应用仍面临经济压力。
- 工艺控制复杂:激光切割需要精确控制能量密度、焦点位置和切割速度等多个参数,工艺复杂性高。
- 热影响区问题:虽然激光切割的无接触特性减少了机械损伤,但热应力带来的热影响区可能对晶圆材料的性能产生不利影响,需进一步优化工艺来减少这种影响。
技术改进方向
为了解决这些问题,研究人员正着力于降低设备成本、提高切割效率和优化工艺流程。
- 高效激光器与光学系统:通过研发更高效的激光器和先进的光学系统,不仅能够降低设备成本,还能提升切割精度和速度。
- 优化工艺参数:深入研究激光与晶圆材料的相互作用,改进工艺以减少热影响区,提升切割质量。
- 智能控制系统:开发智能控制技术,实现激光切割过程的自动化和智能化,提高切割过程的稳定性和一致性。
激光切割技术在超薄晶圆和高精度切割场景中表现尤为出色。随着晶圆尺寸的增大和电路密度的提升,传统机械切割方法难以满足现代半导体制造对高精度和高效率的需求,而激光切割因其独特的优势,正逐渐成为这些领域的首选方案。
尽管激光切割技术仍面临设备成本和工艺复杂性等挑战,但其在高精度、无接触损伤方面的独特优势使其成为半导体制造领域的重要发展方向。随着激光技术和智能控制系统的不断进步,激光切割在未来有望进一步提升晶圆切割的效率与质量,推动半导体产业的持续发展。
|